We offer 24-hour chat support
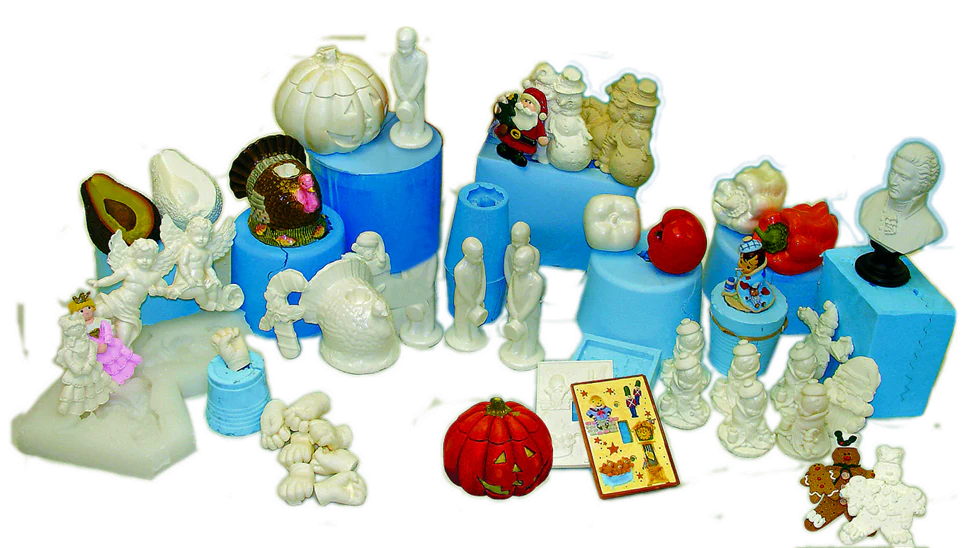
Complete Beginner's Guide to Resin Casting
Welcome to our comprehensive beginner's guide to resin casting! Whether you're a creative enthusiast or someone looking to explore a new hobby, resin casting offers endless possibilities for creating unique and custom pieces. In this step-by-step guide, we will take you through the fascinating world of resin casting, from understanding the basics to mastering different techniques and ensuring your safety throughout the process.
Resin casting involves pouring epoxy resin or polyurethane resin, a two-component system consisting of resin and hardener, into molds and allowing it to cure. The result is a durable, high-gloss, and clear surface that can be used for various applications, such as jewelry, home decor, and even sculptures. With resin casting, you have the freedom to create one-of-a-kind pieces that reflect your creativity and personal style.
To get started with resin casting, there are a few essential tools and supplies you'll need, including mixing cups, silicone molds, a heat gun for removing bubbles, and gloves to protect your hands. We'll guide you on choosing the right resin for your project, proper mixing and measuring techniques, and even creating custom molds. We'll also share tips on coloring resin and troubleshooting common issues that may arise.
However, our guide doesn't stop at techniques and tips. Your safety is our top priority. We'll provide you with important safety precautions to follow when working with resin, including working in a well-ventilated area, and wearing protective gear.
Resin casting is a journey that allows you to unleash your creativity and bring your ideas to life. So, get ready to dive into this exciting craft and discover the joy of creating custom pieces that make a statement. Let's embark on this resin casting adventure together!
Key Takeaways:
- Resin casting involves pouring epoxy resin into molds to create durable and glossy custom pieces.
- Essential tools and supplies for resin casting include mixing cups, molds, heat gun, and gloves.
- Choosing the right resin and mastering mixing and measuring techniques are crucial for successful casting.
- Creating custom molds allows for endless design possibilities.
- Removing bubbles and coloring resin are techniques that enhance the result.
- Ensuring safety precautions throughout the process is essential for a risk-free experience.
- Resin casting offers a world of creativity and the opportunity to create unique pieces.
What is Resin Casting?
Resin casting is a versatile technique that allows you to create stunning and durable objects with epoxy or polyurethane resin such as KastEZ Resin from EnvironMolds. This two-component system consists of resin and hardener, which are mixed and poured into molds. As the resin cures over time, it hardens into a high-gloss, clear surface that is both visually appealing and long-lasting.
Resin casting has found applications in various industries, including flooring, furniture, and industrial manufacturing. However, it has also gained significant popularity in the art and crafting community. Artists and creatives now use resin casting to make unique jewelry pieces, intricate home decor, and captivating sculptures.
With resin casting, the possibilities are endless. You can experiment with different molds, colors, and techniques to bring your creative visions to life. The versatility of epoxy resin allows for intricate details, vibrant pigments, and a smooth, professional finish.
Applications of Resin Casting
Epoxy resin casting has become a preferred choice for many projects due to its remarkable properties. Its durability makes it suitable for creating functional items like tabletops and coasters, while its high-gloss, clear surface enhances the aesthetic appeal of decorative pieces. Here are some common applications of resin casting:
- Artistic sculptures and figurines.
- Jewelry and accessories.
- Customized home decor and furniture accents.
- Resin paintings and mixed media art.
- Embedded objects and mementos.
Resin casting provides a platform for expressing your creativity and bringing your ideas to life. Whether you're a beginner or an experienced artist, exploring resin casting opens a world of artistic possibilities.
Essential Tools and Supplies for Resin Casting
When it comes to resin casting, having the right tools and supplies is crucial for a successful and enjoyable experience. Here are the essential items you'll need to get started:
- Mixing Cups: Mixing cups are used to accurately measure and combine resin and hardener. Look for cups with clear markings to ensure precise measurements.
- Silicone Molds: Silicone molds are perfect for creating a variety of shapes and designs. They are flexible, durable, and allow for easy removal of the cured resin.
- Heat Gun: A heat gun is an indispensable tool for eliminating bubbles in resin. By applying heat, the bubbles rise to the surface and pop, leaving you with a bubble-free finish.
- Gloves: It's important to protect your hands when working with resin. Opt for disposable gloves that fit comfortably and provide good dexterity.
Remember: Safety should be a top priority when working with resin and its associated tools. Always wear gloves and work in a well-ventilated area to minimize exposure to fumes.
Recommended Tools and Supplies
In addition to the essentials, here are some recommended tools and supplies that can further enhance your resin casting process:
- Measuring Scale: A precise measuring scale helps ensure accurate measurements of resin and hardener, especially for larger projects.
- Mixing Sticks: Stirring sticks or wooden craft sticks are ideal for mixing resin thoroughly and evenly.
- Pigments and Colorants: Add a personal touch to your resin creations with pigments and colorants. Experiment with different colors to achieve unique effects.
- Mold Release Spray: Mold release spray helps in easy removal of the resin from the molds, preventing any damage to the molds or the final piece.
- Resin Sealant: A resin sealant can be applied to finished resin pieces to provide a glossy and protective coating, enhancing their durability and shine.
With these tools and supplies at your disposal, you'll be well-equipped to embark on your resin casting journey.
Tool/Supply |
Description |
Mixing Cups |
To accurately measure and combine resin and hardener. |
Silicone Molds |
For creating a variety of shapes and designs. |
Heat Gun |
To eliminate bubbles in resin. |
Gloves |
To protect hands from resin and ensure safety. |
Measuring Scale |
For precise measurements of resin and hardener. |
Mixing Sticks |
For thoroughly and evenly mixing resin. |
Pigments and Colorants |
To add color and uniqueness to resin projects. |
Mold Release Spray |
To facilitate easy removal of resin from molds. |
Resin Sealant |
To provide a glossy and protective coating for finished pieces. |
Choosing the Right Resin for Your Project
When it comes to resin casting, the type of resin you choose plays a crucial role in the outcome of your project. There are different types of resin available, each with its own unique properties and advantages. Understanding these options will help you make an informed decision and achieve the desired results.
Types of Resin
- Clear Resin: Clear resin is ideal when you want the final result to be transparent. It provides a high-gloss, glass-like finish, making it perfect for jewelry, decorative items, and artwork where clarity is essential. Clear resin allows you to showcase intricate details and embedded elements, creating a visually stunning piece.
- Pigmented Resin: Pigmented resin offers the ability to add colors and create unique effects in your projects. With a wide range of pigments available, you can achieve vibrant colors, subtle hues, or even create marbled or swirl patterns. Pigmented resin is perfect for adding a pop of color to jewelry, creating colorful resin art, or making custom-colored home decor items.
Considerations for Choosing Resin
When selecting the right resin for your project, there are a few factors to consider:
- Transparency: Determine if you want a transparent or colored result. Clear resin is suitable for transparent or translucent projects, while pigmented resin allows for various color options.
- Project Requirements: Think about the specific needs of your project. Consider factors such as UV resistance, flexibility, and heat resistance if applicable.
- Curing Time: Different types of resin have varying curing times. Some resins cure faster than others, so choose the one that aligns with your project's timeline.
- Manufacturer Recommendations: Always follow the manufacturer's guidelines and instructions for each resin type. They provide valuable information on mixing ratios, curing time, and any specific considerations for successful results.
Comparison Chart: Clear Resin vs. Pigmented Resin
Factors |
Clear Resin |
Pigmented Resin |
Transparency |
Transparent, high-gloss finish |
Semi-transparent to opaque, depending on color intensity |
Color Options |
N/A |
Wide range of vibrant colors |
Visual Effect |
Enhances clarity and showcases embedded elements |
Offers colorful and unique effects |
Project Types |
Jewelry, decorative pieces, embedded objects |
Colorful resin art, custom-colored items |
By analyzing the specific requirements of your project and considering the advantages of clear resin and pigmented resin, you can confidently choose the resin that best suits your needs. Remember to follow proper mixing and curing techniques to ensure a successful resin casting process.
Proper Resin Mixing and Measuring Techniques
When it comes to resin casting, proper resin mixing and measuring techniques are essential for achieving successful results. Whether you're a beginner or an experienced caster, following these techniques will ensure that your resin cures properly and your final project turns out exactly as you envision.
Most resins used for casting require equal parts of resin and hardener to be mixed. This equal ratio is crucial for the resin to cure effectively. To achieve the perfect mix, it's important to measure the components accurately. Use graduated measuring cups or scales to ensure precise measurements.
Once you have measured the resin and hardener, it's time to combine them. Pour both components into a clean mixing container. It's best to use a container with high walls to prevent any overflow when mixing.
Thorough mixing is key to ensure a proper chemical reaction between the resin and hardener. Use a stir stick or a mixing tool specifically designed for resin casting. Start by scraping the sides and bottom of the container to incorporate any unmixed resin. Then, mix the components in a gentle, folding motion to avoid introducing air bubbles.
Continue mixing until the resin and hardener are fully blended and the mixture appears uniform. Take your time and ensure that there are no streaks or clumps in the mixture. This step is crucial to prevent any inconsistencies in the curing process.
Remember, different resins may have specific instructions provided by the manufacturer. Always refer to these instructions for the recommended mixing ratios and techniques for the specific resin you are using.
Proper resin mixing and measuring techniques are fundamental to resin casting success. By measuring accurately and blending the components thoroughly, you'll create a resin mixture that cures evenly and produces high-quality results for your projects.
Creating Custom Molds for Resin Casting
While pre-made silicone molds for resin casting are readily available, creating custom molds opens a world of possibilities for your creative projects. With custom molds, you have the freedom to design and shape your resin pieces according to your unique vision. Whether you want to create intricate jewelry or one-of-a-kind home decor items, DIY molds allow you to bring your ideas to life.
There are various materials you can use to make your own custom molds. Silicone molds are a popular choice due to their flexibility, durability, and ease of use. They can capture even the finest details of your design, ensuring a high-quality finished product.
Hot Glue Molds
Another option is using hot glue to create molds. This method is especially useful for simple and less intricate designs. Hot glue molds are cost-effective and can be easily crafted to suit your specific project requirements.
To get started with creating custom molds, follow these steps:
- Choose the material for your mold, such as silicone or hot glue.
- Prepare your design or object that you want to mold.
- Apply a release agent or mold release spray to the object to prevent the resin from sticking.
- Position the object in a container and secure it in place.
- Pour silicone or hot glue over the object, ensuring that it completely covers the object and fills any gaps or crevices.
- Allow the mold to be cured according to the manufacturer's instructions.
- Once cured, carefully remove the mold from the container and gently separate it from the object.
With your custom mold ready, you can now start resin casting and bring your creative ideas to life. Get ready to create unique and personalized resin pieces that reflect your style and artistic vision!
Techniques for Bubble-Free Resin Casting
One of the challenges in resin casting is the presence of bubbles, which can mar the result. Fortunately, there are several effective techniques to ensure bubble-free resin casting. By using the right tools and methods, you can achieve a smooth and professional finish for your resin creations. Let's explore the techniques that will help you eliminate bubbles and enhance the quality of your resin casts.
1. Heat Gun for Surface Bubbles
A heat gun is a handy tool for removing surface bubbles from resin. After pouring the resin into your mold, gently pass the heat gun over the surface of the resin. The application of heat causes the bubbles to rise and pop, resulting in a bubble-free surface. Be careful not to hold the heat gun too close or for too long in one spot, as excessive heat can damage the resin or cause it to cure unevenly.
2. Vacuum Chamber for Trapped Air
A vacuum chamber is a fantastic tool for removing trapped air bubbles from resin. Place your resin-filled mold inside the vacuum chamber and activate the vacuum pump. As the air pressure decreases, any trapped air bubbles within the resin rise to the surface, where they can be easily popped or released. This technique ensures thorough bubble removal and leaves you with a flawless resin cast.
3. Pressure Pot for Compressed Resin
A pressure pot is another excellent option for achieving bubble-free resin casting. The pressure pot creates a controlled environment of increased pressure, which compresses the resin and forces air bubbles out. Pour your resin into a mold, then place the mold inside the pressure pot along with a surrounding bag or bladder filled with a liquid that does not interact with the resin. Seal the pressure pot and apply pressure according to the manufacturer's instructions. The increased pressure will compress the resin, resulting in a bubble-free cast.
By experimenting with these techniques, you can perfect your bubble removal process and ensure that your resin casts have a professional, flawless finish. Whether you choose to use a heat gun, a vacuum chamber, or a pressure pot, each technique offers its own advantages and gives you more control over the bubble removal process.
Remember to practice proper safety precautions when using heat guns, vacuum chambers, and pressure pots. Wear the appropriate protective gear, provide adequate ventilation in your workspace, and carefully follow the manufacturer's instructions to maintain a safe resin casting environment.
Tips for Coloring Resin for Creative Projects
Coloring resin allows you to add a personal touch to your projects. Whether you want to create vibrant jewelry, unique home decor, or captivating art pieces, adding color to your resin casts can enhance their visual appeal. There are various colorants available for resin, each offering different effects and intensity. Let's explore some tips for coloring resin and creating stunning colorful creations.
Resin Dyes
Resin dyes are highly concentrated colorants specifically formulated for resin casting. They offer intense and vibrant colors, allowing you to create eye-catching designs. Resin dyes come in a wide range of shades, from bold primaries to shimmering metallics, giving you endless possibilities for your resin projects. To achieve the desired color intensity, start by adding a small amount of resin dye and gradually increase the amount until you achieve the desired shade. Remember to follow the manufacturer's instructions for the specific resin dye you are using.
Pigments
Pigments are another popular option for coloring resin. They come in powder or liquid form and offer a more opaque and solid color effect. Pigments can be mixed and blended to create custom shades, allowing you to experiment and achieve unique color combinations. When using pigments, start with a small amount and gradually add more until you reach your desired hue. Keep in mind that pigments can sometimes settle at the bottom of the resin, so make sure to mix thoroughly to distribute the color evenly.
Experiment and Mix Proportions
When it comes to coloring resin, don't be afraid to experiment and play with different proportions. Adding more colorant will result in a more pronounced and intense color, while using less will create a more translucent effect. Take the time to mix small batches of resin with different color concentrations to see how they turn out. This will give you a better understanding of how the color will appear once the resin cures. Remember to keep a record of your color formulas if you plan on replicating specific shades in the future.
Additionally, consider the transparency of the resin you are using when choosing your colorants. Clear resin allows the color to shine through, while tinted or opaque resin may alter the final hue. It's always a good idea to do a small test cast before committing to a larger project to ensure the color meets your expectations.
Now that you have a better understanding of coloring resin, you can unleash your creativity and bring your projects to life with vibrant and captivating colors. Experiment with different colorants, mix proportions, and create beautiful resin creations that reflect your personal style.
Ensuring Safety when Working with Resin
When it comes to resin casting, safety should always be a top priority. By taking the necessary precautions, you can protect yourself and create a safe working environment. Here are some essential safety measures to follow:
1. Work in a Well-Ventilated Area
Resin emits fumes during the curing process, which can be harmful if inhaled in large quantities. It's crucial to work in a well-ventilated area or use a ventilation system to ensure proper airflow. This will help to minimize exposure to fumes and promote a safer working environment.
2. Wear Protective Gear
When working with resin, it's important to wear protective gear to safeguard yourself from potential hazards. Always wear gloves to protect your skin from direct contact with resin, as it may cause irritation or allergic reactions. Additionally, consider wearing a respirator mask to filter out any airborne particles or fumes.
3. Avoid Direct Contact with Resin
Resin can be sticky and may cause skin irritation upon contact. To prevent this, avoid direct skin contact with resin by wearing gloves. In the event of accidental contact, wash your hands thoroughly with soap and water. If irritation persists, seek medical advice.
4. Properly Dispose of Resin Waste
Resin waste should be disposed of responsibly to avoid environmental contamination. Follow local regulations and guidelines for proper disposal methods. Do not pour excess resin or resin-contaminated materials down the drain or dispose of them in regular trash bins. Instead, consult your local waste management facility for appropriate disposal options.
5. Keep Resin Casting Materials Secure
Resin casting materials should be stored securely and out of reach of children and pets. Keep them in a designated area away from food, drinks, and other household items to prevent accidental ingestion or contamination.
6. Educate Yourself on Safety Precautions
Stay informed about safety precautions and practices related to resin casting. Familiarize yourself with the specific safety guidelines provided by the manufacturer of the resin you are using. By staying educated and up to date, you can ensure a safer resin casting experience.
Remember, safety should always come first when working with resin. By following these safety precautions, you can enjoy the creative process of resin casting with peace of mind.
Resin Casting Safety Precautions |
Work in a well-ventilated area |
Wear protective gear (gloves, respirator mask) |
Avoid direct contact with resin on the skin |
Properly dispose of resin waste |
Store resin casting materials securely |
Educate yourself on safety precautions |
Common Resin Casting Issues and Troubleshooting
Sometimes, resin casting can come with its fair share of issues. Resin casters may encounter problems such as sticky resin, air bubbles, and uneven curing. However, rest assured that these common challenges can be resolved using proper troubleshooting techniques.
Troubleshooting Sticky Resin
Sticky resin can be frustrating, but there are effective solutions. One important step is to mix the resin thoroughly, ensuring that the resin and hardener are combined evenly. Additionally, applying heat to the resin can help it cure and harden properly, resolving the stickiness. Use a heat gun or a heat source recommended by the resin manufacturer to gently warm the surface of the resin. This will aid in the curing process and eliminate the stickiness.
Resolving Air Bubbles
Air bubbles are a common issue in resin casting, but don't worry, they can be eliminated. One technique is to pour the resin carefully, starting from one corner of the mold and gradually filling it to minimize the introduction of air. Use a heat gun to gently pass over the surface of the resin or use a vacuum chamber to remove any trapped air bubbles. Both methods help release the air from the resin, resulting in a smooth and bubble-free finish.
Addressing Uneven Curing
Uneven curing can occur when the resin doesn't set evenly, resulting in areas that are partially cured or remain tacky. To troubleshoot this issue, ensure that you are following the proper resin mixing ratios and thoroughly mix the resin and hardener according to the manufacturer's instructions. Uneven curing can also be caused by temperature or humidity variations. Consider moving your resin casting process to a controlled environment to maintain consistent conditions. If the issue persists, consult the resin manufacturer for further guidance.
By understanding and applying these troubleshooting techniques, you can overcome common issues that arise during resin casting. Make sure to follow the specific instructions provided by the resin manufacturer and experiment with different methods to find the best solutions for your projects.
Conclusion
Congratulations! You've reached the end of this beginner's guide to resin casting. Throughout this guide, we've covered the basics of resin casting, including the tools and supplies you'll need, the various techniques for successful casting, and the importance of safety precautions.
Now that you have a good understanding of resin casting, it's time to unleash your creativity and dive into your own resin projects. Whether you're interested in making unique jewelry pieces, designing stunning home decor, or creating one-of-a-kind art, resin casting offers endless possibilities for expressing your creativity.
Remember to let your imagination guide you as you experiment with different colors, styles, and shapes. With resin casting, you have the power to bring your creative visions to life. Let your passion for crafting and your love for resin projects ignite your artistic journey. Enjoy the process and have fun exploring the world of resin casting!
FAQ (Frequently Asked Questions) :
What is resin casting?
Resin casting is a technique that involves pouring epoxy resin, a two-component system consisting of resin and hardener, into molds and allowing it to cure. The resin gradually hardens to form a durable, high-gloss, clear surface.
What tools and supplies do I need for resin casting?
Essential tools and supplies for resin casting include mixing cups, silicone molds, a heat gun for removing bubbles, and gloves to protect your hands.
How do I choose the right resin for my project?
When choosing resin for your project, consider the specific requirements. Clear resin is ideal for transparent results, while pigmented resin allows you to add colors and create unique effects.
What is the proper resin mixing and measuring techniques?
Most resins require equal parts of resin and hardener to be mixed. Accurate measurement and thorough mixing are crucial for a proper chemical reaction and a fully cured result.
Can I create my own molds for resin casting?
Yes, you can create your own molds using materials like silicone or hot glue. This allows you to create unique shapes and designs for your resin projects.
How can I achieve bubble-free resin casting?
To eliminate bubbles, you can use a heat gun to pop surface bubbles, a vacuum chamber to remove trapped air, or a pressure pot to compress the resin and force out any bubbles.
How can I color resin for my projects?
You can use resin dyes or pigments to color resin. Resin dyes offer intense colors, while pigments provide a more opaque and vibrant effect. Follow the manufacturer's instructions and experiment with proportions for desired color intensity.
What safety precautions should I take when working with resin?
It's important to work in a well-ventilated area, wear protective gear such as gloves and a respirator mask, and avoid direct contact with resin on your skin.
What are some common resin casting issues and how can I troubleshoot them?
Sticky resin can be fixed by thorough mixing and applying heat, while air bubbles can be eliminated by careful pouring, using a heat gun or vacuum chamber. Troubleshooting techniques can help resolve issues like uneven curing.
How to Make Molds for Resin
- Design and Model Preparation: Start by selecting the object you wish to duplicate. Prepare it by ensuring it's clean and free of any debris.
- Select Mold Material: Silicone is the most popular material for making molds due to its flexibility, durability, and ease of use. It can capture fine details and allows for easy demolding without damaging the cast or the mold.
- Create a Mold Box: This will contain the silicone or your chosen mold-making material around your model. It can be made from cardboard, plastic, or wood, tailored to fit closely around your model with some space for the mold material.
- Mix and Pour Mold Material: Follow the instructions for your silicone or mold-making material. Mix thoroughly to ensure a consistent mixture without bubbles and pour it over your model in the mold box, ensuring it's completely covered.
- Cure and Demold: Allow the mold material to cure as per the manufacturer's instructions. Once cured, carefully remove the mold from the mold box and gently extract the original model, leaving you with a mold ready for resin casting.
Materials Used for Resin Molds
- Silicone is the preferred material for resin molds due to its flexibility, reusability, and non-stick properties.
- Polyurethane rubber can also be used but is less common due to its sensitivity to moisture and potential for bubbles.
- Latex and vinyl are other options but less durable and versatile compared to silicone.
Using Concrete in Resin Molds
- Yes, you can use concrete in resin molds, especially if the mold is made of silicone. Silicone molds are versatile enough to handle materials like concrete, plaster, and more, besides resin.
Using Plastic as a Mold for Resin
- Plastic can be used as a mold for resin, especially if the plastic is rigid and non-porous. However, the success depends on the type of plastic and its compatibility with the resin. Smooth, non-stick plastics like HDPE or certain types of polypropylene work best.
Using Hot Glue Instead of Resin
- Hot glue can be used for crafting and small projects but does not have the same properties or durability as resin. It's not suitable for applications where the clarity, strength, or longevity of resin is required.
Alternatives to Traditional Molds for Resin
- Everyday objects like bowls, boxes, and packaging can be used as molds for resin if they are made of non-porous materials.
- Balloons, textured fabrics, or even sand can be used to create unique shapes and textures in resin art.
Best Resin for Molds
- The "best" resin depends on your project requirements:
- Epoxy resin is versatile, has excellent clarity, and is relatively easy to work with, making it great for beginners and detailed casts.
- Polyurethane resin cures faster and is more cost-effective for larger projects but can be more sensitive to moisture and may not be as clear as epoxy.
- UV resin cures quickly under UV light, suitable for small projects and jewelry.
Leave a comment